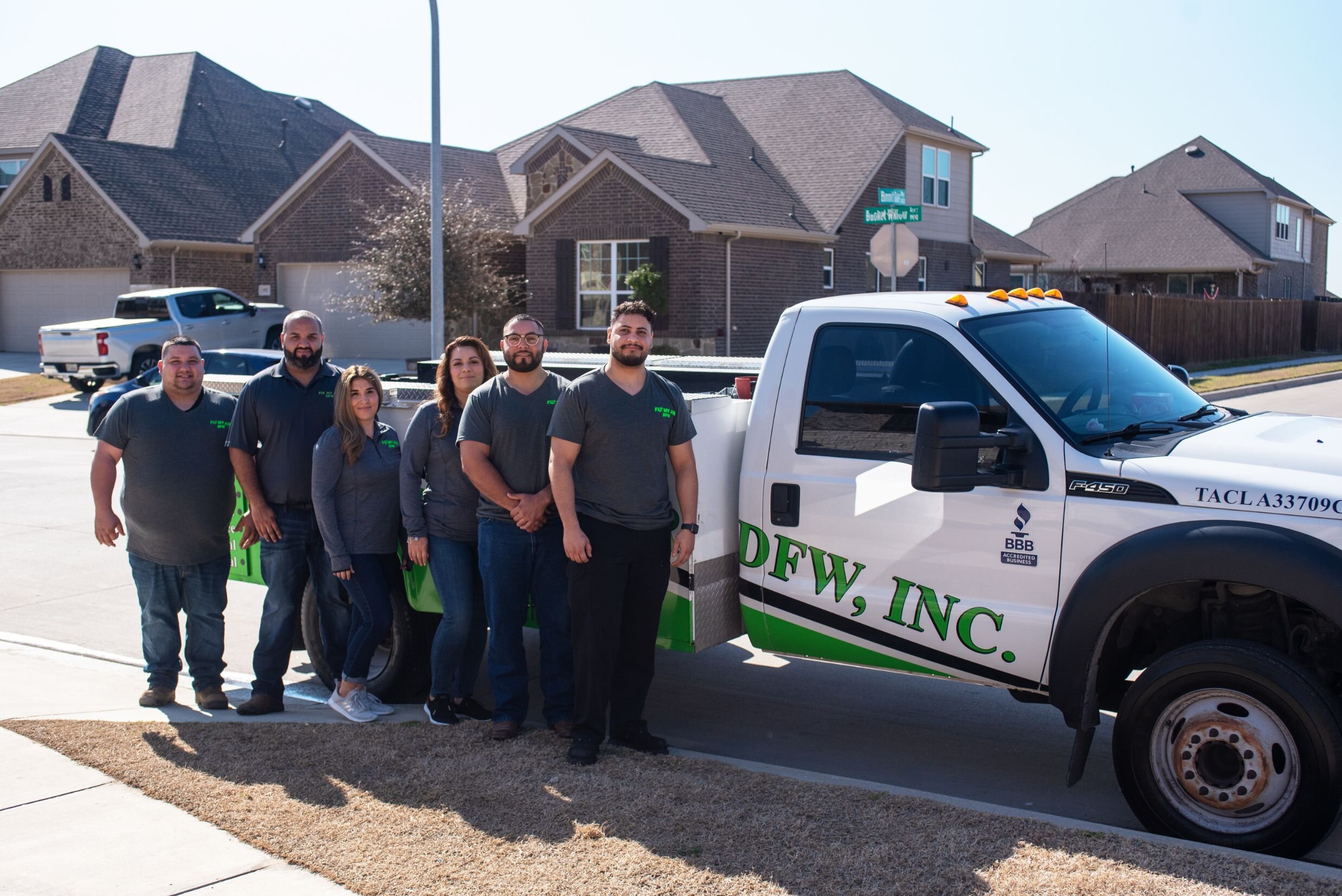
Commercial HVAC Repair in Fort Worth
We Serve Fort Worth, Saginaw, Blue Mound, Lake Worth, Keller, Haslet, Watauga, Richland Hills, North Richland Hills, Justin, Hurst, Euless, Bedford, Colleyville, Southlake, and Grapevine
Commercial HVAC systems are crucial in maintaining comfortable and productive environments for businesses in Fort Worth. These systems are made to handle larger spaces and more complex heating, cooling, and ventilation requirements than residential units. Routine maintenance and quick repairs are essential to keep commercial HVAC systems running efficiently and prevent costly downtime.
-
When issues arise, professional commercial HVAC repair services in Fort Worth offer specialized expertise to diagnose and resolve problems quickly. Common issues include refrigerant leaks, compressor failures, electrical malfunctions, and airflow problems. Experienced technicians use state-of-the-art tools to pinpoint the problem's source and implement effective solutions. Repairs may involve replacing worn components, recharging refrigerant levels, cleaning or replacing filters, and calibrating control systems. Professional repair services also prioritize energy efficiency, helping businesses cut down on operating costs and minimize their environmental impact.
Choosing a reliable commercial HVAC repair service in Fort Worth is critical for maintaining optimal indoor air quality and comfort in commercial spaces. Search for companies with a notable track record of servicing various commercial HVAC systems, including rooftop units, chillers, and complex multi-zone systems. Prompt response times, 24/7 emergency services, and comprehensive maintenance plans are valuable features to consider. By partnering with a reputable commercial HVAC repair provider, businesses can maintain comfortable environments for employees and customers while protecting their investment in essential building infrastructure.
Signs Commercial HVAC Repair Is Needed in Fort Worth, TX
-
Inconsistent temperatures across different areas of a commercial space indicate potential HVAC issues. Some zones may feel too warm while others remain cold, creating discomfort for occupants. This problem often stems from ductwork leaks, malfunctioning thermostats, or imbalanced airflow. Promptly addressing uneven temperature distribution can improve overall comfort, enhance energy efficiency, and prevent strain on specific system components. Professional diagnosis and repair can restore uniform temperature control throughout the facility.
-
A sudden upward swing in energy costs without corresponding changes in usage patterns signals potential HVAC inefficiencies. Aging systems, clogged filters, or malfunctioning components can cause the HVAC system to work harder, consuming more energy. Regular maintenance and timely repairs help maintain optimal energy efficiency. Identifying and addressing the root cause of increased energy usage can lead to considerable cost savings and improved system performance. A professional assessment can pinpoint efficiency issues and recommend appropriate solutions.
-
Reduced airflow from vents indicates potential blockages, ductwork issues, or fan problems. Weak airflow can result in inadequate cooling or heating, creating uncomfortable conditions for occupants. Common causes include dirty filters, obstructed ducts, or malfunctioning blower motors. Quickly addressing airflow problems can prevent further system damage and improve indoor air quality. Professional inspection and cleaning of ductwork and necessary repairs can restore proper airflow and system efficiency.
-
Strange sounds emanating from the HVAC system, such as banging, rattling, or whistling, often indicate mechanical issues. These noises may result from loose components, worn bearings, or refrigerant leaks. Ignoring unusual noises can lead to more severe damage and costly repairs. A prompt, professional inspection can identify the noise's source and address the underlying problem. Timely repairs prevent further wear on components and maintain system reliability.
-
Frequent on-off cycles of the HVAC system, known as short cycling, indicate potential issues with thermostat settings, refrigerant levels, or electrical components. Short cycling strains the system, reduces efficiency, and shortens equipment lifespan. This problem can result in inadequate temperature control and increased energy consumption. A professional diagnosis can identify the cause of short cycling and implement appropriate repairs. Rapidly addressing this issue helps maintain system longevity and optimal performance.
Our reviews
Our Commercial HVAC Repair Process
-
Initial Assessment
The repair process begins with a comprehensive evaluation of the commercial HVAC system. Experienced technicians inspect visible components, review maintenance history, and discuss concerns with facility managers. This assessment helps identify potential problem areas and guides further diagnostic efforts. Technicians consider system age, recent performance issues, and specific client concerns. The first assessment creates a foundation for developing an effective repair strategy.
-
Diagnostic Testing
Advanced diagnostic tools and techniques pinpoint specific HVAC issues. Technicians may use thermal imaging cameras, refrigerant pressure tests, and electrical diagnostics to identify malfunctions. This thorough approach helps uncover hidden problems that may not be apparent during visual inspections. Accurate diagnosis leads to more targeted and efficient repairs, minimizing downtime and reducing costs. The results of diagnostic testing inform the comprehensive repair plan's development.
-
Component Repair or Replacement
Technicians proceed with necessary repairs or component replacements based on diagnostic results. This procedure may involve fixing electrical connections, sealing refrigerant leaks, or replacing worn parts. High-quality replacement components are used to maintain system integrity and performance. Technicians follow manufacturer specifications and the best practices in the industry during repairs. Clear communication with facility managers regarding repair options and costs helps make informed decisions about the most appropriate solutions.
-
System Calibration
The HVAC system is carefully calibrated to operate at peak efficiency following repairs. This process involves adjusting thermostat settings, balancing airflow, and fine-tuning control systems. Proper calibration optimizes energy efficiency and guarantees consistent performance across all zones. Technicians may use specialized software and tools to achieve precise calibration. This step is critical for maximizing the advantages of repairs and maintaining long-term system health.
-
Final Inspection
A thorough final inspection is conducted to verify the effectiveness of repairs and calibration. Technicians test all system functions, monitor performance metrics, and confirm proper operation. Any remaining issues are addressed before concluding the repair process. Facility managers are provided with detailed documentation of repairs and recommendations for future maintenance. The final inspection offers assurance that the HVAC system is operating safely and efficiently, ready to meet the facility's heating and cooling needs.
Fix My Air DFW stands out as a top choice for reliable commercial HVAC repair services in Fort Worth and surrounding areas.
With experienced technicians, state-of-the-art diagnostic tools, and a commitment to minimizing business disruptions, Fix My Air DFW delivers efficient and effective solutions for all commercial HVAC needs. Business owners and facility managers seeking professional HVAC expertise can trust Fix My Air DFW to provide prompt, high-quality repairs that keep commercial spaces comfortable and operations running smoothly.